ThrowBack Thursday (TBT): No Cue Tone
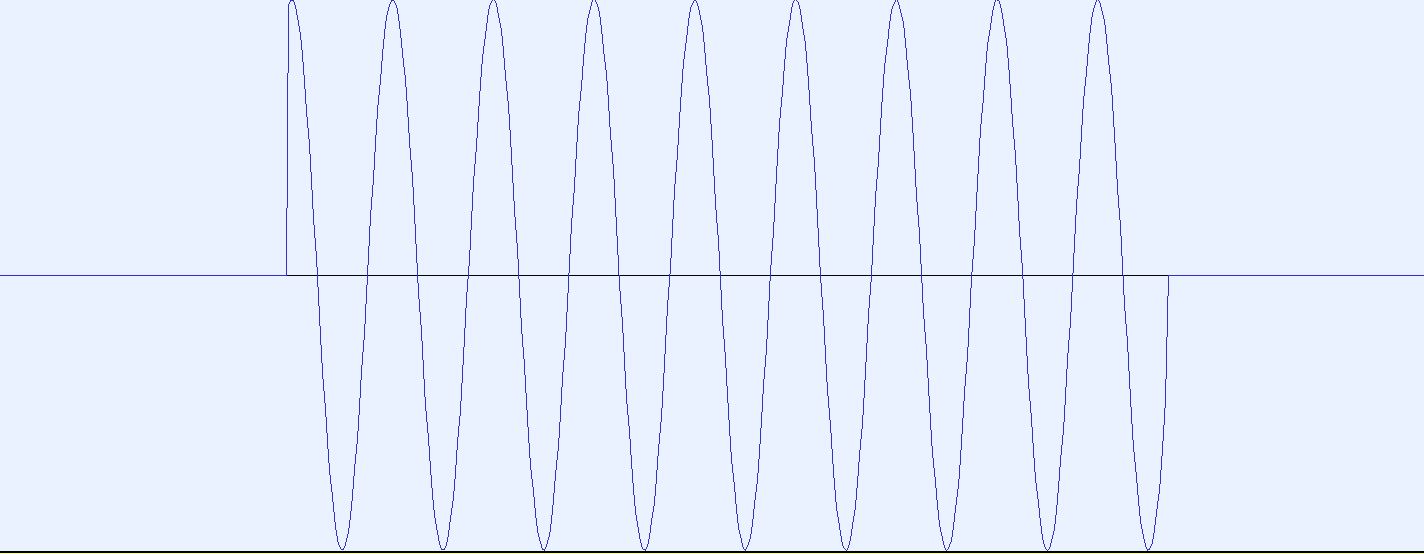
The case of the false information.
When troubleshooting any system and people are involved in providing feedback, an expert technician knows how to differentiate between good and wrong information. In my experience, I found that operators of machines, particularly in a production environment where they may be paid by how many units they produce, tend to give general, and sometimes misleading, information about a problem. It’s not their fault; they wouldn’t need the technician if they knew about the machines.
One famous example of this is when I worked at Magnetix, an audio cassette, VHS, duplicator, and CD/DVD replicator. The audiocassette master machines that played back the 1-inch master tape at speeds up to 80-times operating speed in a loop had a white piece of “cue tone” tape spliced in at a specific location where it duplicated an extremely low-frequency tone onto the slave tape. The tape loading machines later used this tone to determine where the tape recording ended, and that’s where it would splice in the leader and drop the tape. If the tape didn’t have the cue tone, the cassette loading machine would error, and it caused a lot of headaches. So, the duplication operators learned how to check for the cue tone, which helped alleviate loading issues that could come many days after the operators duplicated the tape.
What happens when there’s “no cue tone”? The operator gives this specific information and nothing further because they’re busy running production lines and don’t have the time. In a sense, they’re trusting the technician and all their wisdom to figure out what that means.
Here is just a sample of what “no cue tone” really means:
- The master tape cue length is too short. A mastering problem;
- The bulb in the CDS sensor is blown. A once every two-years problem;
- A bad optoisolator on the input of the cue signal. A once in 5-years problem;
- Oxide residue on the sensor window. An operator problem as they’re supposed to clean the machines periodically on long runs and between jobs. Some duplication runs can go on for days, and the operator has enormous faith in just letting the machine run.
- Cue/Audio amplifier problem. A technician problem. I found that the issue is likely with a tantalum capacitor. One failed about every 6-months.
- BNC connector problem. A technician problem; due to vibration, if non-soldered connectors are used, these will eventually fail. Replace with solderable connectors.
- Capstan pinch-roller problem-Usually limited to one machine at a time. The capstan sets the speed of the tape, and the pinch-roller, made of either rubber or polyester (or is it Nylon?), holds the tape to the capstan. Slippage here causes the tape to run fast or slow, changing the frequency of the cue tone. Capstan pinch-rollers have problems of their own, not limited to:
- faulty bearings from oxide contamination;
- rubber degradation as sulfur content is reduced over time, leading to a sticky roller;
- Vibrations cause solenoid misalignment over time.
These are the issues that come to mind when I remember the operator telling me “no cue tone”. The potential problems are varied, and an experienced technician knows what to look for even if all the information they have before them is three words. Understanding the system and observing it will tell you everything else you need to know.
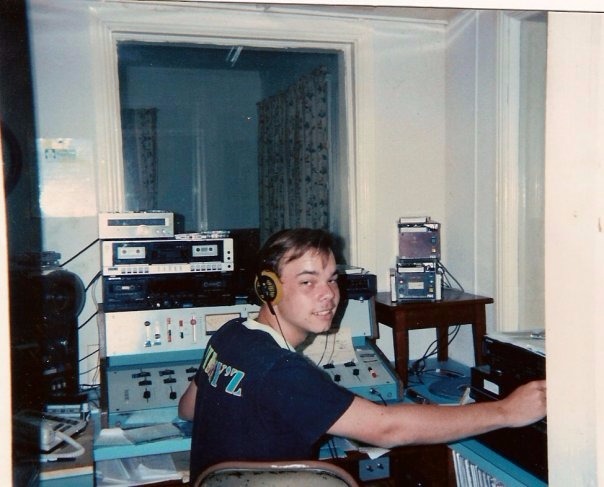
It all started when I watched my dad fix a very expensive RC car after I ran it to death, when I was a kid.